Why plastic extrusion is perfect for mass production
Why plastic extrusion is perfect for mass production
Blog Article
Key Benefits and Considerations of Executing Plastic Extrusion in Your Tasks
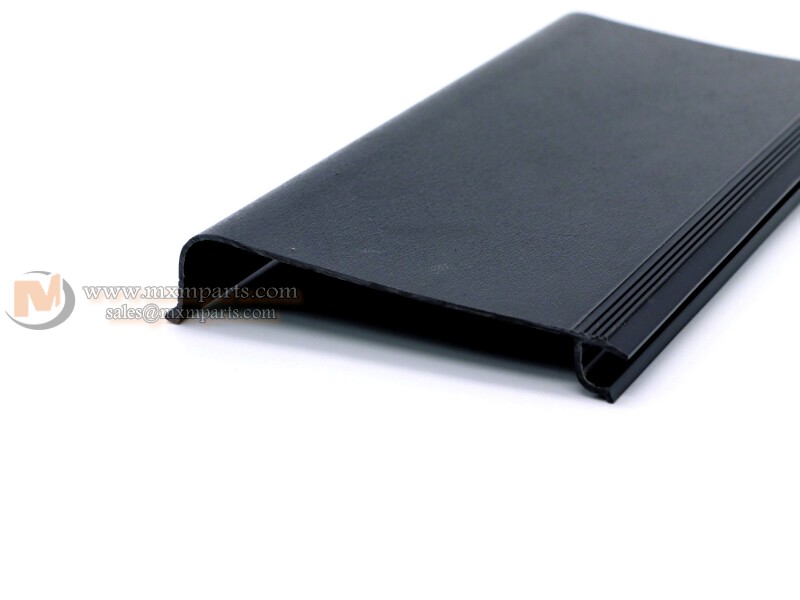
Comprehending the Fundamentals of Plastic Extrusion
Plastic extrusion, a staple in the production industry, is a procedure that entails melting raw plastic material and improving it right into a continual account. This account, once cooled, can be cut right into wanted sizes or curled for later usage. The appeal of plastic extrusion lies in its flexibility. A variety of items, from piping to window frames, can be generated. The process needs an extruder, an elaborate device with a warmed barrel, a rotating screw, and a die at the end. The plastic product, in the form of pellets, is fed into the extruder, where it's melted and compelled via the die, taking its shape. The selection of plastic and the layout of the die identify the item's features.
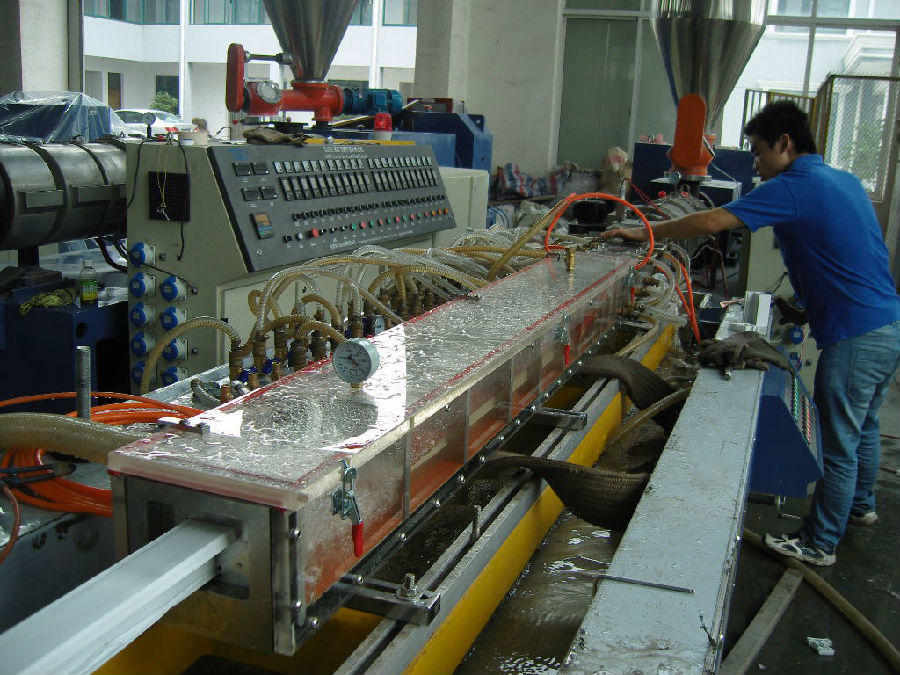
The Economic Advantage of Plastic Extrusion
The financial benefit of plastic extrusion exists primarily in 2 areas: cost-effective material manufacturing and useful manufacturing rates. With plastic extrusion, companies can create high volumes of material at a lower expense compared to various other approaches. Furthermore, the procedure flaunts an excellent production speed, substantially lowering time and additional enhancing its economic stability.
Cost-efficient Product Manufacturing
A substantial benefit of plastic extrusion is its remarkable cost-effectiveness. This manufacturing procedure allows for constant, high-volume production with minimal waste, which equates right into reduced costs. The raw materials made use of, typically plastic pellets, are fairly low-cost compared to various other materials (plastic extrusion). The process itself requires much less energy than numerous various other production techniques, even more reducing prices. Furthermore, the extrusion procedure permits a high degree of precision in forming the plastic, lowering the need for expensive post-production alterations or corrections. The toughness and long life of extruded plastic items typically suggest less need for substitutes, adding to long-term financial savings. All these factors make plastic extrusion a highly economical option for numerous jobs, offering an eye-catching balance between price and efficiency.
Beneficial Production Speeds
While maintaining the cost-effectiveness of the materials, an additional noteworthy benefit of plastic extrusion exists in its quick manufacturing speeds. This effectiveness in the production procedure is associated to the constant nature of the extrusion process, enabling high-volume production in a relatively brief time period. The rate of production directly associates to a reduction in labor prices and an increase in result, therefore boosting the total economic feasibility of the process. Furthermore, the busy production does not jeopardize the quality of the last item, guaranteeing regular and reputable results. This combination of top quality, rate, and cost-effectiveness emphasizes the considerable economic advantage of applying plastic extrusion in various jobs.
Versatility and Customization: The Toughness of Plastic Extrusion
Among the prominent toughness of plastic extrusion hinges on its versatility and personalization potential. These high qualities unlock to unlimited layout opportunities, providing producers the capability to tailor products to details requirements. This increased level of modification not only improves item functionality but also significantly increases item originality.
Unrestricted Design Possibilities
Plastic extrusion beams in its capacity to provide virtually endless style opportunities. This method gives flexibility to create intricate profiles and intricate shapes, a task tough to accomplish with various other fabrication strategies. Owing to the fluid nature of molten plastic, the procedure is flexible enough to generate a varied variety of types, dimensions, and dimensions. The plastic can be manipulated to match one-of-a-kind specifications, enabling for the manufacturing of tailored geometries and meeting certain customer needs. Plastic extrusion can handle a range of plastic kinds, increasing its application extent. This adaptable technique, for that reason, offers a wide variety of markets from building and construction to auto, product packaging to electronics, and past. With plastic extrusion, the style opportunities are virtually countless.
Boosting Product Uniqueness
The flexibility of plastic extrusion can considerably boost item originality. This procedure enables designers to try out different shapes, dimensions, and shades, offering them the flexibility to produce distinct products that attract attention in the marketplace. It is this modification that offers an unique identity to each item, differentiating it from its competitors.
In addition to its visual benefits, the customizability of plastic extrusion also offers sensible advantages. Designers can change the buildings of the plastic according to the certain requirements of a knockout post the application, enhancing the item's performance. They can make the plastic extra adaptable, much more long lasting, or extra resistant to heat, depending on what the product needs. Hence, plastic extrusion not just improves product originality but additionally its utility and bankability.
Layout Limitations in Plastic Extrusion: What You Need to Know
Just how can design restrictions possibly affect the procedure of plastic extrusion? While plastic extrusion is functional, design limitations can stop its advantages. Specific facility designs may not be practical due to the restrictions of the extrusion procedure, possibly limiting the creation of elaborate accounts. The procedure is less appropriate for multi-chambered or hollow structures. Additionally, the extrusion procedure might not constantly offer the preferred surface area coating, particularly for those requiring high gloss or optical clarity. Material choice can likewise posture obstacles, as not all polymers are suitable for extrusion. High-temperature resistant plastics, as an example, may provide troubles. Recognizing these restraints is vital for reliable implementation of click over here plastic extrusion in your projects. plastic extrusion.
Examining the Ecological Effect of Plastic Extrusion
While recognizing design constraints is a considerable facet of plastic extrusion, it is just as crucial to consider its ecological ramifications. The process of plastic extrusion entails melting plastic materials, potentially releasing unsafe gases into the environment. Further, the resulting items are often non-biodegradable, adding to garbage dump waste. Advancements in modern technology have permitted for even more environmentally-friendly practices. As an example, utilizing recycled plastic products in the extrusion process can reduce ecological impact. In addition, establishing naturally degradable plastic choices can help mitigate waste concerns. Examining these environmental factors is crucial when carrying out plastic extrusion projects, ensuring a balance in between effectiveness, cost-effectiveness, and ecological responsibility.
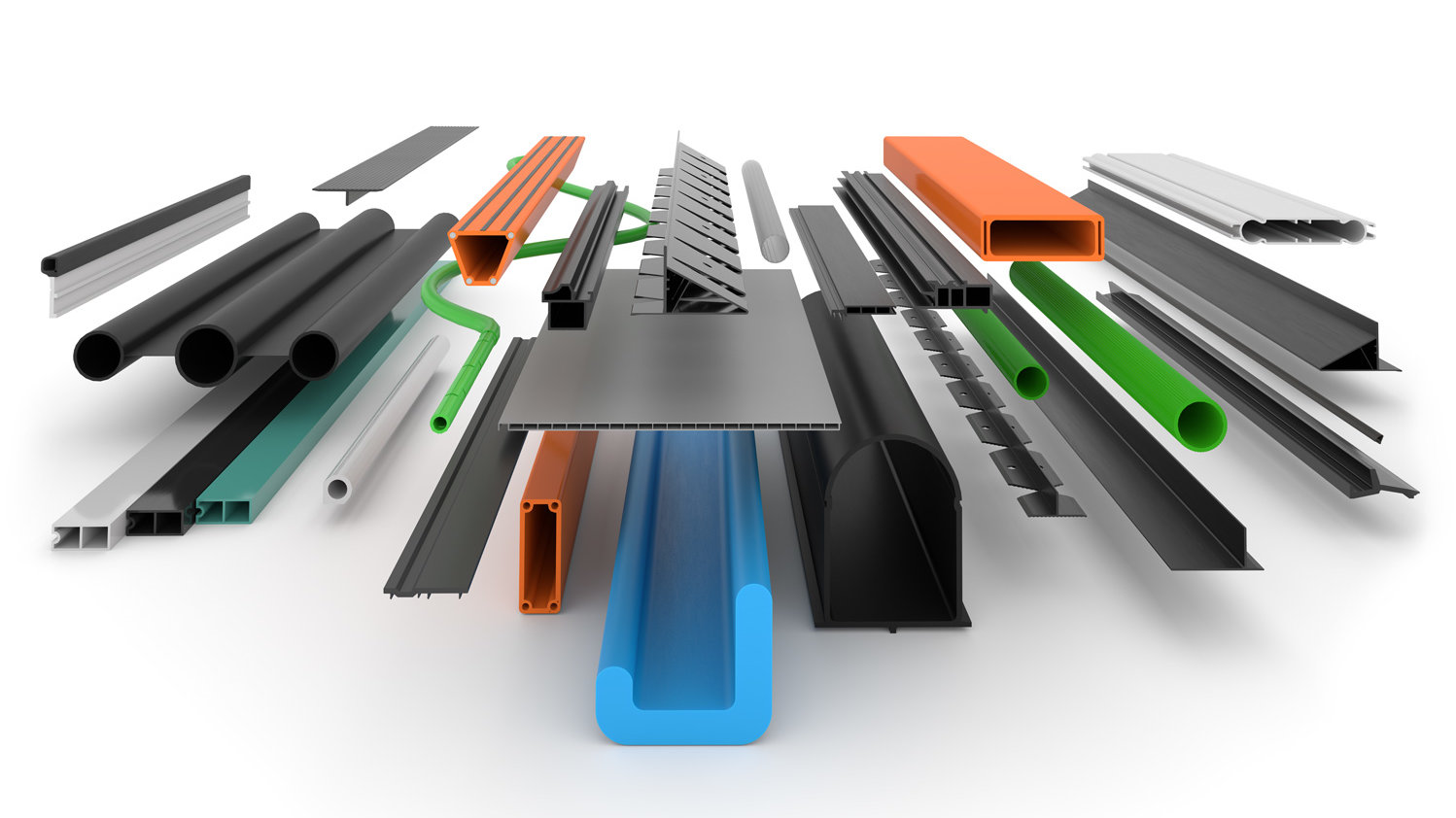
Study: Successful Projects Utilizing Plastic Extrusion
Success tales in the field of plastic extrusion abound, showing both the flexibility and effectiveness of this production process. plastic extrusion. Another effective case is the manufacturing of plastic film for packaging and farming. These instances highlight plastic extrusion's important role in numerous industries, attesting to its flexibility, cost-effectiveness, and reputable output.
Verdict
In final thought, plastic extrusion uses a economical and efficient method for creating complicated shapes with very little waste. Integrating plastic extrusion right into projects visit our website can lead to successful outcomes, as confirmed by many instance researches.
Plastic extrusion, a staple in the manufacturing industry, is a process that involves melting raw plastic material and reshaping it into a continual profile. Plastic extrusion can handle a selection of plastic kinds, expanding its application scope.Exactly how can create limitations possibly affect the process of plastic extrusion? The process of plastic extrusion involves melting plastic materials, potentially releasing dangerous gases into the environment. Using recycled plastic materials in the extrusion process can decrease environmental impact.
Report this page